What if the very materials that shape our world could be reimagined, re-engineered, and redefined? The answer, simply put, lies in the boundless realm of composite materials, offering possibilities that stretch beyond the horizon of conventional design and engineering.
The world of design and manufacturing is in a constant state of evolution, driven by the relentless pursuit of innovation, efficiency, and performance. At the forefront of this evolution stand composite materials, offering a versatile and powerful approach to a wide range of applications. Composite materials are created by combining two or more different materials with different physical and chemical properties. They come in many different forms. These materials are often designed to overcome the shortcomings of the individual materials, resulting in a final product with enhanced characteristics.
Aspect | Details |
---|---|
Definition | Materials engineered from two or more constituent materials with significantly different physical or chemical properties, which remain separate and distinct within the finished structure. |
Composition | Typically composed of a reinforcement material (e.g., fibers like carbon, glass, or aramid) embedded in a matrix material (e.g., polymers like epoxy, polyester, or phenolic resins, or metals). |
Key Advantages | High strength-to-weight ratio; design flexibility; corrosion resistance; tailored properties; durability; reduced part count; potential for manufacturing cost savings. |
Applications | Aerospace (aircraft components, spacecraft), automotive (body panels, structural parts), marine (boat hulls, decks), construction (bridges, buildings), sports equipment (tennis rackets, golf clubs), wind energy (wind turbine blades), and medical devices (prosthetics, surgical instruments). |
Manufacturing Processes | Various techniques including hand lay-up, spray lay-up, compression molding, resin transfer molding (RTM), filament winding, pultrusion, and prepreg processing. |
Types | Fiber-reinforced polymers (FRP), metal matrix composites (MMC), ceramic matrix composites (CMC), and hybrid composites. |
Material Properties of Interest | Tensile strength, compressive strength, flexural strength, impact resistance, fatigue resistance, thermal properties (e.g., coefficient of thermal expansion, thermal conductivity), and resistance to environmental degradation. |
Quality Control | Essential to ensure the structural integrity and performance of composites, incorporating non-destructive testing (NDT) methods like ultrasonic inspection, radiography, and thermography, along with mechanical testing of coupons and finished parts. |
Sustainability | Focus on eco-friendly materials, manufacturing methods, and end-of-life considerations, including recyclability and waste reduction, to mitigate the environmental footprint of composite materials. |
Future Trends | Advancements in material science (e.g., nanomaterials, bio-based resins), automation and digital manufacturing, AI-driven design optimization, and the integration of sensors and smart technologies into composite structures. |
Reference | ScienceDirect: Composite Material |
The collaborative process with designers is paramount. Identifying the right material and manufacturing process is a crucial aspect of project success. This often involves a detailed analysis of the requirements, including the desired mechanical properties, environmental conditions, and cost constraints. Following the selection of materials and processes, a robust design validation and verification plan is established. This plan typically involves a combination of analytical modeling, simulations, and physical testing to ensure the final product meets all performance criteria. The verification process utilizes standard laboratory coupon testing, prototype part evaluation, and functional testing, depending on the application.
One particular area of expertise is in the manufacturing of prepreg materials. There are different approaches to prepreg manufacturing. Designing with composites, specifically, the use of prepreg materials, provides advantages over other manufacturing methods, such as infusion and resin transfer molding, by allowing for more precise control of resin content. Resin systems based on epoxy, melamine, and silicone are commonly used in the facility. These resin systems can be modified to achieve specific characteristics, such as enhanced strength, increased temperature resistance, or improved chemical resistance. The facilities are carefully designed to ensure the quality and consistency of the final product.
One of the notable materials is Ultrex Micarta, which has earned a reputation as a durable and attractive material suitable for knife handles and gun grips. This material is a laminated composite made of paper and cotton fabric reinforced phenolic. This material combines the strength of the fabrics with the binding properties of the phenolic resin, resulting in a robust and visually appealing final product.
The applications for these composite materials are broad and constantly expanding. They are utilized in a wide range of products, from the aesthetic and functional applications such as knife handles and gun grips to highly specialized applications such as cryogenic storage and transportation.
The design of a composite material begins with understanding the specific requirements of the application. This is done by considering the loads the material will be subjected to, the operating environment, and the desired lifespan. The selection of the appropriate materials is crucial, as different reinforcing fibers and matrix materials offer varying properties. For example, cloth reinforcement can provide high strength without the tool wear associated with fiberglass or metal.
Furthermore, the manufacturing process must be optimized to ensure the highest quality. The process of manufacturing prepreg materials involves careful control of resin content and fiber alignment. Quality control measures are implemented throughout the entire process, from raw material inspection to final product testing. This is particularly critical in applications where performance is paramount, such as in the aerospace or automotive industries.
The selection of the material also depends on the desired properties of the final product. The material can be selected based on their application and their history of established laboratory or application. Property comparisons are often used to determine the most appropriate material for a specific application. For example, in the case of cotton sheet products, a property comparison allows for the selection of materials that best meet the performance requirements.
The company, Changzhou Micarta Composite Material Company, is committed to the use of composite materials. They are well-versed in all aspects of composite design and manufacturing. The applications for these materials are vast, ranging from traditional uses such as knife handles and gun grips, to more advanced applications in cryogenic environments. Thermoset composite materials are also used in cryogenic pipeline insulation, support, and in cryogenic storage vessels, bunkering tanks, and LNG carriers.
The ability to customize the materials is another benefit. Different resin systems can be modified to achieve specific characteristics. This customization, combined with a wide range of available materials and manufacturing processes, allows designers to create products with optimized performance characteristics.
The physical dimensions of the finished products are also considered. The minimum internal diameter can be as small as 0.625 inches (1.6 mm), and the maximum outside diameter is typically limited to 5 inches (127 mm). These dimensional constraints can affect the manufacturing processes and the final product designs.
The economics of production are also a critical consideration. All of the production is done with ongoing mass production in mind from the start. This approach ensures that products are not only high-performing but also cost-effective to manufacture on a large scale.
In short, the world of composites offers a unique blend of performance, flexibility, and efficiency. From aesthetic applications such as knife handles and gun grips to cryogenic environments and beyond, these materials are transforming industries and opening up new possibilities. This approach, which combines advanced material science, innovative manufacturing processes, and collaborative design principles, ensures the success of each project.

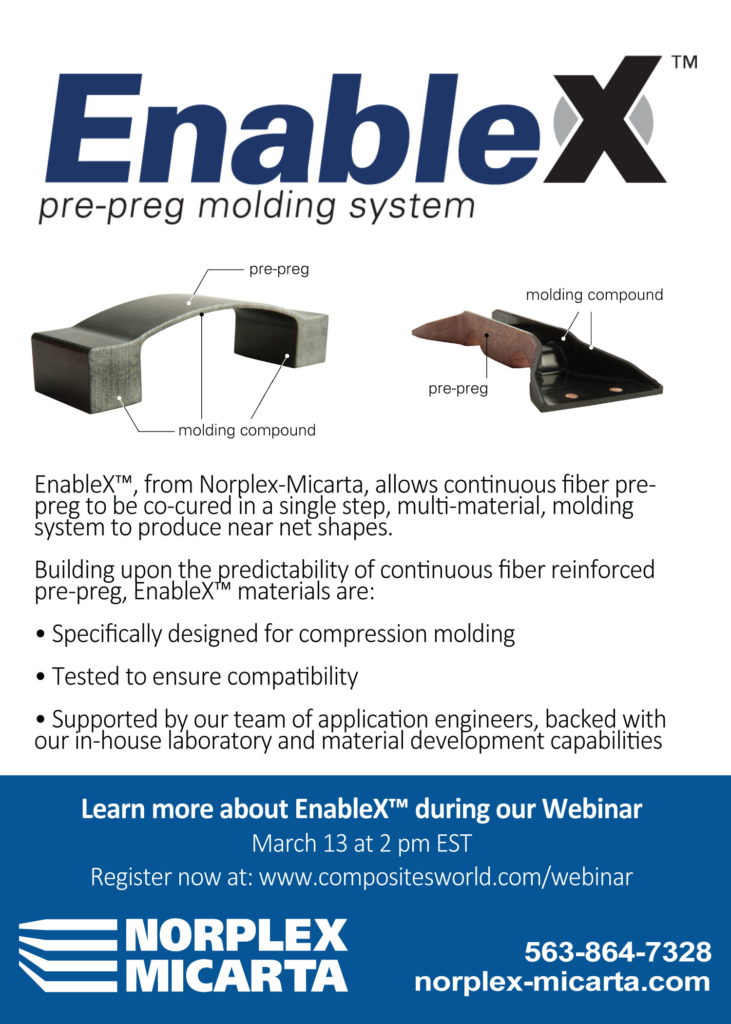
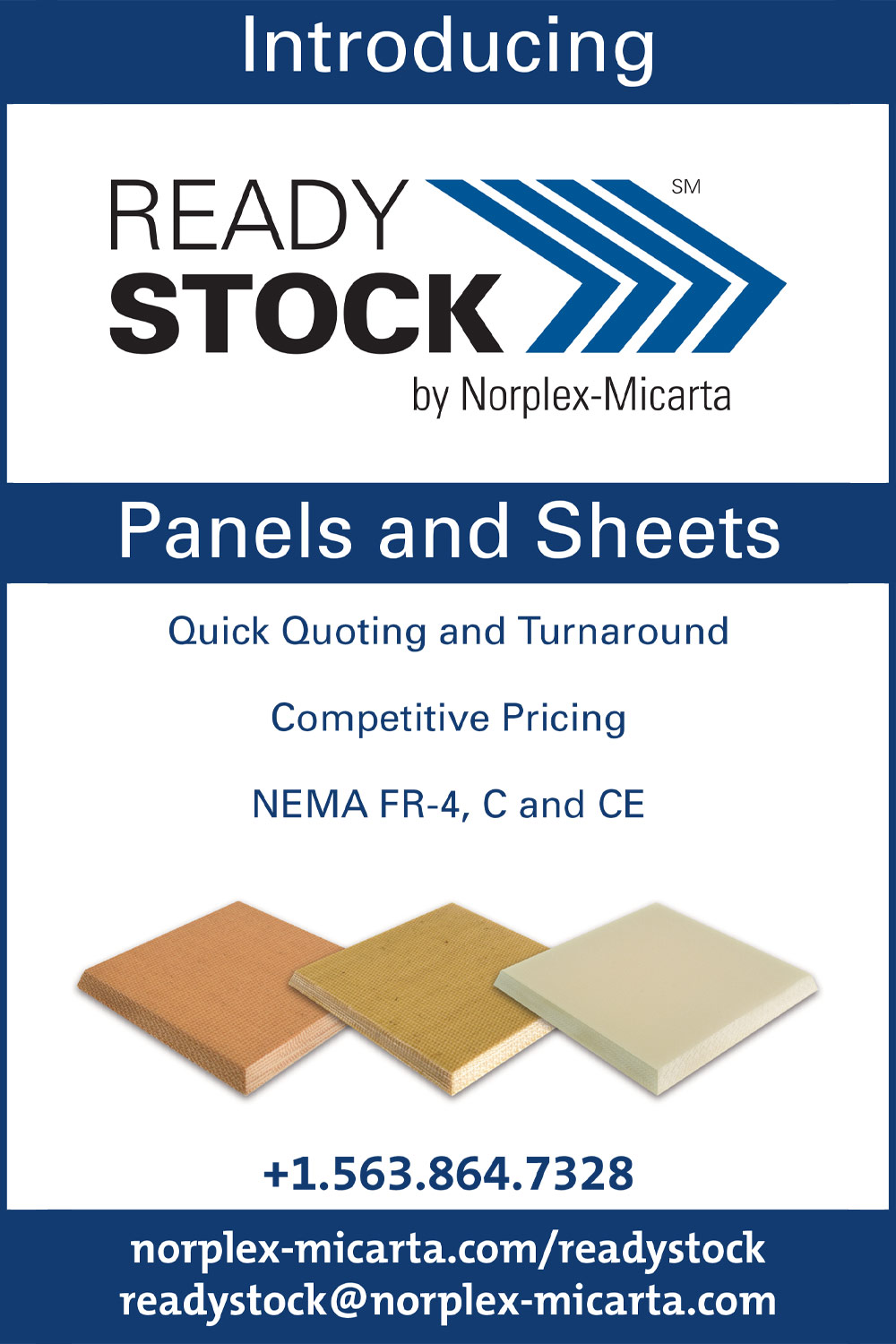